对辊式干法造粒机是一种将干粉物料制成颗粒的设备,广泛应用于化工、制药、食品等行业。以下是一些充分发挥其性能的方法与建议:
物料准备
-物料特性分析:在造粒前,需充分了解物料的粒度分布、湿度、流动性、粘性及压缩性等特性。例如,物料粒度太粗或太细都可能影响造粒效果,可通过筛选或粉碎等预处理手段将物料粒度调整至合适范围,一般要求物料粒度在20-200目之间。
-物料预处理:对于湿度较高的物料,应先进行干燥处理,使其水分含量降低至合适范围,通常以2%-8%为宜,以保证物料的流动性和压缩成型性。同时,可根据物料特性添加适量的助挤剂或润滑剂,如硬脂酸镁、滑石粉等,改善物料的加工性能,减少物料与压辊之间的粘附,提高造粒质量。
设备调整
-辊压调整:根据物料的性质和所需颗粒的强度、密度,合理调整对辊的压力。压力过小,物料难以成型,颗粒强度低;压力过大,可能导致颗粒过硬、设备负荷增加及能耗上升。一般来说,初始辊压可设置在较低水平,然后逐步增加压力,通过观察颗粒的成型情况和质量来确定最佳辊压值。例如,对于一些硬度较高的物料,可能需要较大的辊压,而对于质地较软的物料,较低的辊压即可满足成型要求。
-辊速调整:对辊的转速直接影响物料的进料速度和造粒效率。适当提高辊速可以增加产量,但过高的辊速可能使物料在辊间停留时间过短,导致颗粒成型不佳。通常,辊速应根据物料的流动性和压辊的压力进行调整。对于流动性好的物料,可适当提高辊速;而对于流动性差或粘性较大的物料,则需降低辊速,以保证物料能够充分填充到压辊之间并成型。一般辊速范围在5-20转/分钟。
-间隙调整:压辊之间的间隙决定了颗粒的厚度和密度。间隙过小,颗粒会过于致密,甚至可能出现裂片现象;间隙过大,颗粒则松散易碎。在设备调试时,应先将间隙设置为较大值,然后逐渐减小间隙,同时观察颗粒的厚度和质量,直至达到理想的颗粒效果。一般来说,颗粒的厚度可根据产品要求在1-10毫米之间进行调整。
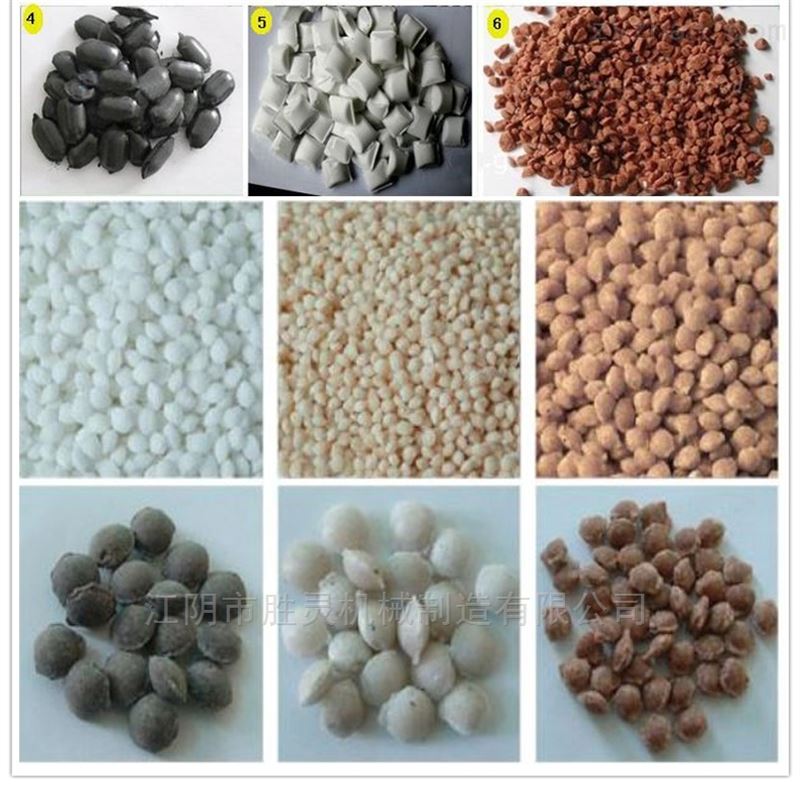
生产操作
-均匀给料:确保物料均匀地输送到对
辊式干法造粒机的进料口,避免物料偏析或局部堆积。可采用定量给料设备,如螺旋给料机、振动给料机等,精确控制物料的给料量和给料速度,使物料在压辊宽度方向上均匀分布,以保证颗粒质量的一致性。
-设备运行监控:在造粒过程中,密切关注设备的运行状态,包括电机电流、轴承温度、压辊压力等参数。若电机电流突然增大,可能是物料进料量过大或压辊压力过高,需及时调整;轴承温度过高则可能表示润滑不良或设备存在异常摩擦,应立即停机检查并排除故障。同时,观察颗粒的成型情况,如颗粒的形状、大小、强度等,如有异常,及时分析原因并进行调整。
-定期维护保养:制定详细的设备维护保养计划,定期对设备进行清洁、润滑、紧固等保养工作。及时清理压辊表面的物料残留和灰尘,防止物料堆积影响造粒效果;定期检查压辊的磨损情况,如发现压辊表面磨损严重,应及时进行修复或更换,以保证压辊的平整度和表面光洁度,从而维持设备的稳定性能和造粒质量。
工艺优化
-批次间一致性控制:对于多批次生产,要确保每批次物料的特性和生产工艺参数保持一致,以实现颗粒产品质量的稳定。建立完善的物料采购和检验标准,以及工艺参数记录和追溯体系,对每批次物料的来源、预处理情况和生产过程中的工艺参数进行详细记录,以便在出现质量问题时能够及时查找原因并进行改进。
-工艺参数优化:通过实验设计和数据分析,不断优化造粒工艺参数。例如,采用正交试验法或响应面分析法等,研究物料特性、辊压、辊速、间隙等因素对颗粒质量的影响规律,确定最佳的工艺参数组合,以提高颗粒的合格率和生产效率。同时,随着生产技术的发展和设备的更新,及时对工艺进行调整和优化,以充分发挥设备的性能优势。
